MUNICH, Germany — ZF unveiled an electric motor that does not require magnets or rare earth materials, reducing reliance on mining in countries such as China and cutting manufacturing's carbon footprint.
In contrast to the magnet-free concepts of separately excited synchronous motors (SESM) already available today, ZF's In-Rotor Inductive-Excited Synchronous Motor, which it calls I 2 SM, transmits the energy for the magnetic field through an inductive exciter inside the rotor shaft. This makes the motor uniquely compact with maximum power and torque density, according to Martin Fischer, a ZF Board of Management member, who met with transportation industry media during the IAA Mobility conference here at the Munich Trade Fair Grounds. Motor Ac Permanent Magnet
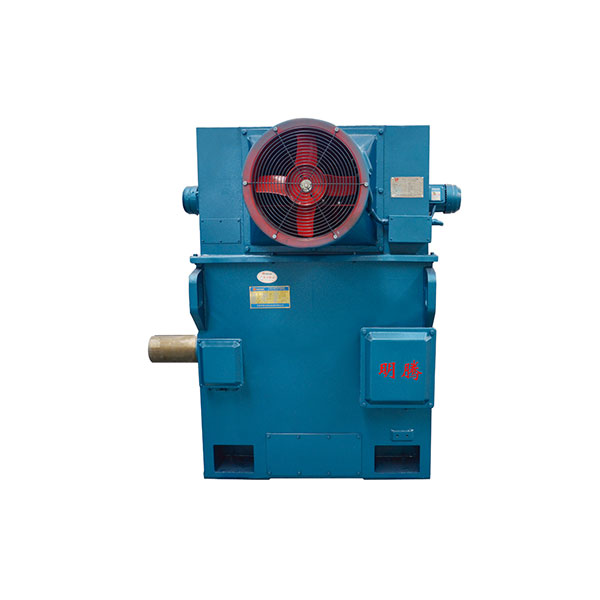
This advanced variant of a separately excited synchronous motor is an alternative to permanent-magnet synchronous machines (PSM), the motors most frequently used in electric vehicles. Those standard motors are based on magnets that require rare earth materials. With the I 2 SM, Fischer said ZF is setting a new standard for making e-motors both extremely sustainable in production and highly powerful and efficient in operation.
See also: Connected vehicles produce vulnerabilities, among them are EV chargers
"With our technology, we can replace the magnets and yet have the same performance as the synchronous machine where the electric current would create a magnetic field as good as magnetic and better than a synchronous machine where the other types of electric meters," Fischer explained.
He added this would have geopolitical benefits, such as not relying on China for the precious metals needed for the magnet motor technology.
"With this magnet-free e-motor without rare earth materials, we have another innovation with which we are consistently improving our electric drive portfolio to create even more sustainable, efficient, and resource-saving mobility," said Dr. Holger Klein, CEO of ZF. "This is our guiding principle for all new products. And we currently see no competitor that masters this technology as well as ZF."
Compared to standard SESM systems, the inductive exciter can reduce losses for the energy transmission into the rotor by 15%. In addition, the CO 2 footprint in production, which arises with PSM e-motors in particular due to magnets, including rare earth materials, can be reduced by up to 50%.
"This uniquely compact electric motor without magnets is impressive evidence of our strategy to make e-drives more resource-efficient and sustainable, primarily through efficiency improvements," said Stephan von Schuckmann, member of the Board of Management of the ZF Group. "We're consistently using efficient 800-volt silicon carbide technology while eliminating rare earths - all without increasing the dimensions or weight."
In addition to the benefits of eliminating rare earth materials in a compact and robust package, the I 2 SM eliminates the drag losses created in traditional PSM e-motors. This enables better efficiency at operations, such as long highway trips at high speed.
To ensure that the magnetic field in the rotor is built up by current instead of magnets, the conventional SESM concepts still require sliding or brush elements in most cases, which force compromises. Those compromises include a dry installation space not accessible for oil cooling that needs additional seals. Because of this, Fischer explained, conventional SESMs take up around 90 mm more space axially, so manufacturers generally cannot flexibly vary between PSM and SESM variants in their model planning without additional effort.
ZF compensated for the design-related disadvantages of common separately excited synchronous machines to offer the advantages of separately excited synchronous machines competitively. In particular, the torque density was significantly increased with an innovative rotor design, according to the company. The space-neutral integration of the exciter into the rotor means no axial space disadvantages and an increase in power density in the rotor leads to improved performance, according to the company.
The technological prerequisite for the ZF innovation is that energy is transferred inductively — or without mechanical contact — into the rotor, generating a magnetic field through coils. Because of this, the I 2 SM does not require any brush elements or slip rings. So there is no longer any need to keep this area dry with seals. As with a permanently magnetized synchronous motor, circulating oil efficiently cools the rotor. Compared to typical separately excited synchronous motors, the ZF innovation requires up to 90 millimeters less axial installation space. In terms of power and torque density, however, the ZF innovation operates at the level of a PSM.
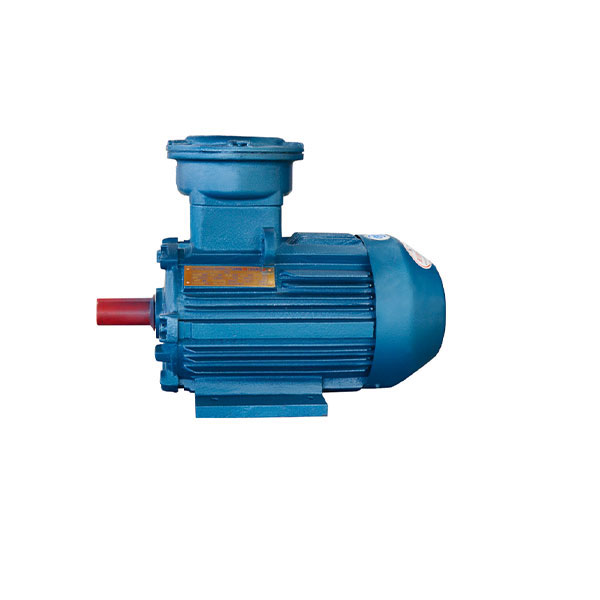
Permanent Magnet Drum Motor For Mining ZF plans to develop the I2SM technology to production maturity and offer it as an option within its e-drive platform. Fischer added that commercial vehicle customers can choose between a variant with 400-volt architecture or with 800-volt architecture for their respective applications. The latter relies on silicon carbide chips in the power electronics.