An exploration of sulfidity calculations, selective delignification, continuous cooking, pulp yield and strength, and control
The history of the kraft pulping process is obscure, and few patents and stories try to explain the origin of this chemical pulping process. Good chelation on metal ions

The story that most likely explain its origin goes back to the 1870s in a soda mill, where a chemical recovery plant operator made a mistake in the process of adding sodium carbonate (Na2CO3) for chemical losses, he added instead sodium sulfate (Na2SO4). The resulting pulp produced with this modification was found to be not only darker than the previous one (i.e., soda pulp) but also stronger. The German and Swedish translation for strength is kraft.
This innovation originated what is currently known as “kraft” or “sulfate” pulping process. The sulfate denomination is because of the addition of sodium sulfate (Na2SO4) in the chemical recovery plant that is also called “salt cake” and is used as a make-up to replace chemical losses.
The sodium sulfate is not the active chemical during the kraft pulping process but only the source to generate sodium sulfide (Na2S). Most of the sodium sulfate in the recovery boiler is reduced to Na2S. The efficiency of this reduction is called reduction efficiency and normal values are in the range of 90–94 per cent. See Equation 1.
Kraft pulp mills are characterized by their unique foul odour that is due mainly to reduced sulfur compounds also referred as TRS (i.e., total reduced sulfur) or non-condensable gases that are generated in the digester and other areas of the recovery cycle (i.e., evaporators, recovery boiler, dissolving tanks, lime kiln, etc). An exhaustive chemical analysis of the TRS gases includes the following important chemical components: methyl mercaptan (CH3SH), dimethyl sulfide (CH3-S-CH3) and dimethyl-disulfide (CH3-SS-CH3), hydrogen sulfide (H2S).
Even though sodium sulfide (Na2S) is generated during the preparation of the kraft cooking liquor (i.e., by reducing the Na2SO4 to Na2S), this chemical does not participate directly in the delignification reactions. Sodium sulfide reacts with water (i.e., in the white liquor) and generates sodium hydrosulfide (NaSH) and sodium hydroxide (NaOH) as in equation 2. The ionized forms are given in equation 3 below.
The active chemicals during kraft pulping are sodium hydroxide (NaOH) and sodium hydrosulfide (NaSH) that degrade and dissolve lignin.
The hydrogen sulfide (HS−) ion improves greatly the selectivity and the delignification rate during kraft pulping by breaking β-O-4 ether linkages in phenolic units of the lignin molecule (Gierer 1985, Svensson 2008, Zhu 2013, Brännvall 2017).
After this breakage, the sulfide ion forms an episulfide unit that subsequently releases elemental sulfur (S°) into the cooking liquor (Gierer 1985, Lindfors et al. 1987). This sulfur partly combines with hydrogen sulfide to form polysulfides that to some extent decomposes into hydrogen sulfide (Zhu 2013, Bränvall 2017). (See Figure 1 at top of page).
Polysulfides decompose at high temperatures (i.e., 170°C) to give sodium thiosulfate that represents part of the sulfur elimination from the cycle (Kubes 1980).
The delignification involves the cleavage (i.e., degradations) of inter-unit linkages (i.e., β-O-4 ether) and the introduction of phenolic hydroxyl groups into the polymer and its fragments (Gellerstedt 1984-a). This explains the hydrophilicity and dissolution of the fragmented lignin in the black liquor. The delignification or the lignin reactions during kraft pulping can be seen as a competition between degradation and condensation reactions. Condensation reactions generate new carbon-carbon bonds that counteract lignin degradation reactions (Gierer 1980).
Sulfidity is the per cent ratio of the sodium sulfide (Na2S) to the active alkali A.A. (i.e., NaOH + Na2S) or to the effective alkali E.A. (i.e., NaOH + ½Na2S), or to the total titratable alkali TTA (i.e., NaOH + Na2S + Na2CO3, etc). The most common ratio is the one calculated with respect to the active alkali (AA) as displayed below in equation 4:
In some mills, the digester operators do not know the definition and/or role of the sulfidity during kraft pulping operations. Then, a white liquor sulfidity level of 32 per cent going down to 30 per cent or even lower to 25 per cent, is usually ignored by the digester operator because of the previous statement.
The above reduction from 32 per cent to 25 per cent (i.e., seven per cent units) might be equivalent to a one to two per cent alkali charge (EAW%) reduction. This sulfidity reduction can drastically affect the delignification power of this white liquor and this change might be equivalent to 3-4 kappa numbers.
In most mills, when the sulfidity drops, the normal reaction of the digester operator is to increase the alkali charge (EAW%) and/or the cooking temperature, but they do not inform the recausticizing operator of this white liquor sulfidity change (i.e., reduction).
Or the other way around, when the recausticizing operator finds a reduction on the white liquor sulfidity, they do not inform the digester operator immediately about this change so that the digester operator should get ready for the corresponding cooking adjustments. Of course, these variations can be resolved quickly and more efficiently (i.e., without human mistake) by using a computerized system to fix these variations using online analyzers.
When referring to the concept of kraft pulping selectivity, this indicates how much lignin is removed in comparison to the amount of the cellulosic material being degraded. The higher the amount of lignin removal, the better is the selectivity of the delignification process.
This selectivity depends mainly on the levels of sodium sulfide in the white liquor that it is used to calculate the corresponding white liquor sulfidities (see equation 4). The selectivity during pulping means the ability to remove lignin from wood without affecting the properties of the carbohydrate components of the fibrous material (Brogdon and Dimmel, 1997).
Sulfidity plays an important role on the rate of delignification and the net effect is the breakage of the β-O-4 bonds of lignin as well as methyl groups, the latter leading to the formation of mercaptans that are responsible for the characteristic odours of kraft mills. The ether β-O-4 linkages are easily broken while the carbon-carbon bonds are more difficult to break and represent a minor portion of lignin fragmentation (Gierer 1985).
Pulp research in the 1980s was focused on finding a selective lignin removal during pulping called extended delignification to minimize the formation of chlorinated aromatic compounds (i.e., toxic dioxins, etc.) during bleaching.
This work conducted to modifications of the kraft process, called “modified continuous cooking” or “modified kraft cooking,” was based on four principles developed at the Royal Institute of Technology and the Swedish Pulp and Paper Research Institute. These principles include: the hydroxide ion concentration [HO−] should be leveled out, the hydrogen sulfide ion concentration [HS−] should be as high as possible throughout the cook, the concentration of dissolved lignin should be as low as possible and the temperature should be low during the whole cook (Annergren 2014).
Results of previous research showed that extending the delignification to lower kappa numbers led to lower pulp yield and pulp of inferior quality (Sjoblom 1983). Current benefits of higher selectivity obtained by modified continuous cooking are not used for extending cooking but for finishing the kraft cooking process at kappa numbers between 27 to 32 for bleachable softwood pulp and 15 to 20 for hardwood pulp.
The sulfidity levels when pulping hardwoods has always been lower than that used for softwoods. When pulping hardwoods, the benefits of sulfidities above 20 per cent are marginal. Sulfidity levels for softwoods in the range of 25 to 30 per cent is considered desirable for bleachable grades (MacDonald 1969). Higher sulfidity levels around 40 per cent are being used (i.e., Sweden) but special attention should be given to the digester metallurgy, as higher sulfidity levels are very corrosive.
It is recommended not to increase sulfidity above 50 per cent for softwoods or above 35 per cent for hardwoods because the increase of the delignification rate is negligible (Brännvall 2017). However, increasing the sulfidity to very high levels around 80 per cent has indeed positive effects on delignification.
Increasing the sulfidity from 35 up to 80 per cent increased the delignification rate by a factor of two and reduced the cooking time by half (Olm et al. 2009). Some researchers have indicated that there is no benefit by increasing the sulfidity indefinitely (Macdonald 1969).
Sulfidity does not increase pulp yield. The hydrogen sulfide (HS−) ion improves greatly the selectivity and the delignification rate during kraft pulping, but do not have any direct effect on protecting the cellulosic material (i.e., chemically increasing pulp yield).
Due to its profound effect on the delignification rate, the HS− ions leads to shorter cooking times to get a target kappa number that favours to less exposure time for cellulosic degradation reactions. This shorter cooking time equates to less exposure time to drastic alkali and/or cooking temperatures and consequently increasing pulp yield. Furthermore, the lower degradation of the fibres can be perceived as better pulp strength.
Around 90 per cent of residual lignin in softwood kraft pulp is chemically bound to carbohydrates mainly to hemicelluloses (Lawoko 2003). The pulp yield losses during pulping explain that by removing more residual lignin there is also an additional removal of hemicelluloses (i.e., xylans). It is believed or assumed that lignin and the cellulosic materials must be linked together even in a standing tree and ultimately removing residual lignins will definitely affect the removal of more xylans.
Sulfidity does not increase pulp yield. The hydrogen sulfide (HS−) ion improves greatly the selectivity and the delignification rate during kraft pulping, but do not have any direct effect on protecting the cellulosic material (i.e., chemically increasing pulp yield).
This partially explains the theory behind the usage of enzymes (i.e., xylanases) for delignification. In this particular case, xylanases do not work directly on the lignin removal but on the very selective degradation of xylan leaving the lignin more exposed to the attack of the bleaching chemicals. A true enzyme for delignification is a ligninase but at this moment there is not such an enzyme for industrial economical applications.
The best chemicals improving the delignification rate are HS− ions (i.e., sulfidity) and anthraquinone-AQ (i.e., very few mills are still using it). It is worth mentioning another digester additive such as polysulfides (PS) that do protect directly the cellulosic material and increase pulp yield. In terms of pulp yield, AQ and PS do increase pulp yield.
AQ is the only digester additive that increases the delignification rate (i.e., shorter cooking time) and protects the cellulosic material (i.e., direct chemical protection) giving higher pulp yield. The last group of digester additives to mention is the surfactants with not enough data to support their positive effect on delignification or cellulosic protection. The only benefit of surfactants as digester additives seems to be the removal of wood extractives for pitch control. See Figure 2.
There are three liquors flowing in a kraft recovery cycle: white liquor (i.e., liquor containing active cooking chemicals NaOH and Na2S), black liquor (i.e., liquor containing degraded organics and inorganics after cooking) and green liquor (i.e., is the dissolved smelt of sodium carbonate, sodium sulfide, etc from the recovery boiler). The most common and important chemicals in the chemical recovery cycle are the following: sodium hydroxide (NaOH), sodium sulfide (Na2S), sodium carbonate (Na2CO3), and sodium sulfate (Na2SO4). See Figure 3.
The great selectivity of the sulfidity is better observed at the beginning of the cooking stages especially during the bulk delignification (i.e., higher lignin removal) but it is less effective at the end of the cooking for removing the residual lignin. When trying to reach the lowest levels of residual lignin the best option is to increase the alkali concentration instead of increasing the hydrogen sulfide concentration (Brännvall 2017). Removal of the residual lignin (i.e., slow-reacting lignin) is a very complex operation that needs special attention.
The main objective of a kraft pulping process is to liberate the fibres in the wood by chemically degrading and dissolving lignin (i.e., ideally); however, other wood components (i.e., cellulose and hemicelluloses) are degraded at the same time and pulping conditions must be controlled in order to obtain high pulp yield and high pulp strength.
Even though, the delignification rate is reduced when approximately 95 per cent of the original lignin in wood has been removed; however, the rates of degradation and dissolution of the carbohydrates continues more or less unaffected (Bränvall 2017). Then the limitations for full delignification are determined by the amount of the slow-reacting residual lignin and by the degree of degradation of the cellulosic material.
The residual lignin is characterized as very slow-reacting polymer, with high content of guaiacyl-lignin units (i.e., resistant), with more complex lignin structure, with more carbon-carbon bonds and highly condensed. Condensation reactions lead to the formation of alkali-stable linkages, thereby increasing the molecular size of lignin fragments. At low residual alkali the fragmented lignin re-condenses and re-precipitates onto the pulp at the bottom of the digester. It is very difficult to remove this condensed lignin from the fibres (Gellerstedt 1984-b).
Sulfidity reduction during kraft pulping has been forced mainly because of environmental pressure and government regulations. Many original kraft mills located close or in the middle of a town have been required to lower or eliminate their odour emissions (i.e., total reduced sulfur – TRS). An additional and important reason for reducing the sulfidity is the advantage of reducing the recovery boiler corrosion.
A sulfur balance it is necessary in order to monitor the sulfur losses (i.e., air emissions) and their impact on the sulfidity of the white liquor and make-up chemical calculations and replacements.
A way to control sulfidity levels is to purge electrostatic precipitator ash from the recovery boiler (Andersson 2014). Current liquor cycles in the kraft pulping process are highly closed and only a small fraction of the chemicals leak. These closed systems help to comply not only with strict environmental limits but also to reduce the cost of make-up chemicals.
Andersson, P., (2014) “A dynamic Na/S balance of a kraft pulp mill.” Master thesis. Karlstad University.
Annergren, G. and Germgård, U., (2014) “Sulfate cooking – a commercially dominating and continuously improving pulping process.” Research Report. Karlstad University.
Brännvall, E., (2017) “The limits of delignification in kraft pulping.” BioResources 12(1): 2081-2107.
Brogdon, BN and Dimmel, DR, (1997) “A TAPPI Press anthology of published papers 1977-1996 – Anthraquinone pulping.”TAPPI Press Atlanta 1997. Edited by Gopal C. Goyal.pp. 100-1485-4
Gellerstedt, G. and Lindfors, E-L., (1984-a) “Structural changes in Lignin during kraft cooking Part 4. Phenolic hydroxyl groups in wood and kraft pulps.” Svensk Papperstid. 87(15): 115-118.
Gellerstedt, G. and Lindfors, E-L., (1984-b) “Structural changes in Lignin during kraft pulping.” Holzforschung 38: 151-158.
Gierer, J., (1980) “Chemical aspects of kraft pulping.” Wood Science and Technology, 14: 241-266.
Gierer, J., (1985) “Chemistry of delignification.” Wood Sci. & Technol., 19: 289-312.
Kubes, G.J., Fleming, B.I., MacLeod, J.M., Bolker, H.I., (1980) “Alkaline pulping with additives – A review.” Wood Sci. Technol., 14: 207-228.
Lawoko, M., Henriksson, G., and Gellerstedt, G., (2003) “New method for the quantitative preparation of lignin-carbohydrate complex from unbleached softwood kraft pulp: Lignin-polysaccharide networks I.” Holzforschung 57(1): 69-74.
Lindfors, E.-L., Gellerstedt, G., Teder, A., and Tormund, D., (1987) “The distribution of different sulfur compounds in kraft cooking.” Paris, Int. Symp. Wood Pulp Chem., pp. 167-170.
Macdonald, R.G., (1969): Pulp and Paper Manufacture, Vol. I, 2nd edition. “The Pulping of Wood.” Joint Textbook Committee of the Paper Industry. TAPPI. pp 414, 420.
Olm, L., Tormund, D., and Lundqvist, F., (2009) “High sulphidity kraft cooking.” Nordic Pulp and Paper Research Journal 24(4): 433-439.
Sjöblom, K., Hartler, N., Mjöberg, J., and Sjödin, L., (1983) “A new technique for pulping to low kappa numbers in batch pulping: Results of mill trials.” Tappi J. 66(9): 97-102.
Svensson, S., (2008) “Minimizing the sulphur content in Kraft lignin.” M.Sc. thesis, STFI-Packforsk. Sweden.
Zhu, W., (2013) “Equilibrium of lignin precipitation.” Thesis for the degree of Licentiate of Engineering. Chalmers University of Technology. Gothenburg, Sweden.
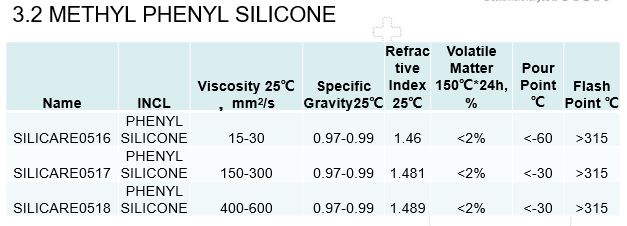
Textile Chemicals And Auxiliaries Augusto Quinde is president of AQuinde Pulping Consulting in Vancouver.